From Fibres to Fences: The Step-by-Step Creation of Durable GRP Fencing
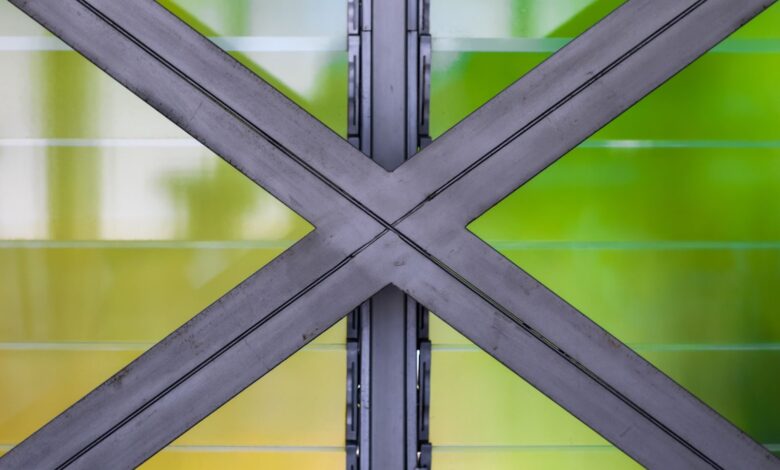
Glass Reinforced Plastic (GRP) fencing has become a popular choice across various industries in the UK due to its exceptional strength, durability, and low maintenance requirements. Understanding the intricate process of creating GRP fencing, from raw fibres to the finished product, reveals why this material is so highly regarded.
The Manufacturing Process of GRP Fencing
1. Material Preparation
The journey of GRP fencing begins with the preparation of raw materials. The primary components are glass fibres and a polymer resin. These materials are chosen for their strength and resilience. The glass fibres provide the structural reinforcement, while the polymer resin acts as the binding agent that holds the fibres together.
2. Pultrusion Process
The most common method for producing GRP fencing is the pultrusion process, a continuous manufacturing technique that ensures consistency and high quality. Here’s a step-by-step breakdown of this process:
Fibre Arrangement: The glass fibres are arranged into a specific pattern and pulled through a resin bath. This arrangement ensures that the fibres are thoroughly saturated with the resin, creating a strong and cohesive material.
Forming and Shaping: After saturation, the fibres and resin mixture is pulled through a heated die, which shapes the material into the desired profile. This step is crucial as it determines the final shape and size of the GRP fencing components.
Curing: As the material passes through the die, it is heated to initiate the curing process. This process solidifies the resin, bonding the fibres together to create a rigid and durable structure. The controlled temperature and curing time ensure optimal strength and longevity.
Cutting and Finishing: Once the material is cured, it is cut to the required lengths and finished to remove any imperfections. This final step ensures that the GRP fencing components meet the exact specifications and quality standards.
Applications of GRP Fencing
GRP fencing is utilised in a variety of settings due to its robust properties and adaptability. In industrial environments, GRP fencing provides a reliable barrier that can withstand harsh conditions, including exposure to chemicals and extreme weather. Coastal areas, such as the Port of Liverpool, benefit from GRP’s resistance to corrosion, ensuring long-lasting performance despite the saline atmosphere.
In the transportation sector, the London Underground has adopted GRP fencing to enhance safety and reduce maintenance costs. The non-conductive nature of GRP makes it an ideal choice for areas with high electrical hazards, providing an added layer of security for both workers and passengers. Residential and commercial properties also use GRP fencing for its aesthetic versatility, allowing customisation in colour and design to match various architectural styles.
Wrapping Up
The creation of GRP fencing, from raw glass fibres to the finished product, involves a meticulous process that ensures exceptional quality and durability. The extrusion process, combined with the inherent properties of GRP, results in a material that is strong, versatile, and low maintenance. This makes GRP fencing an excellent choice for various applications across the UK, from industrial sites to public infrastructure.
Engineered Composites UK, with nearly 35 years of experience, specialises in procuring and distributing GRP pultruded structural profiles, rods, tubes, grating, flooring, and rebar. The company ensures the highest quality by adhering to stringent ISO 9001 standards, offering products that meet exacting specifications for consistency and longevity. By choosing GRP fencing from trusted suppliers like Engineered Composites, businesses can benefit from a reliable and sustainable fencing solution that stands the test of time.