Key Considerations When Selecting Flanges For Different Environments
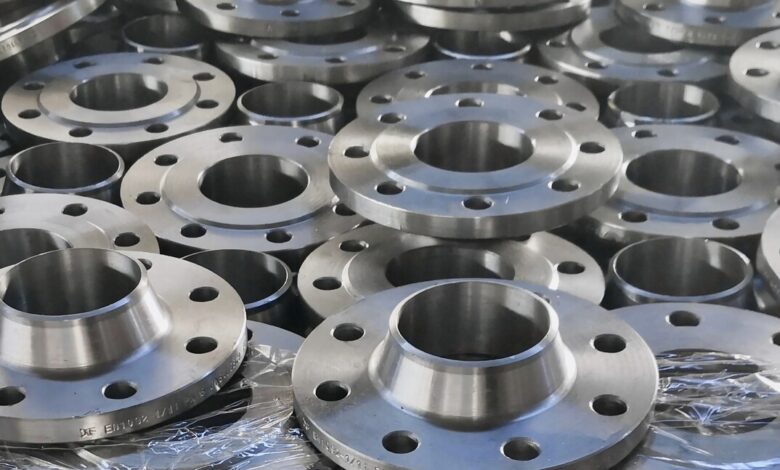
Flanges are very important parts of industrial plumbing systems because they make it easier to connect and disconnect pipes and also provide structural support and leak-proof seals. It is very important to choose the right flange for the climate in order to keep the piping system safe, efficient, and long-lasting.
Flanges are flat, circular discs with evenly spaced holes for bolts, designed to join sections of pipe or to connect pipe to various components such as valves, pumps, or other equipment. They are critical for maintaining the integrity of the piping system, and ensuring it operates smoothly and safely under varying conditions.
Factors To Consider
1. Material Selection
The choice of material for Hastelloy C22 Flanges depends largely on the environment in which they will operate. Common materials include:
Carbon Steel: Suitable for general industrial applications where moderate pressure and temperature conditions are expected.
Stainless Steel: Highly recommended for places that need to fight corrosion, like chemical plants and marine uses.
Alloy Steel: Offers enhanced strength and durability, suitable for high-pressure and high-temperature environments like refineries and power plants.
Non-Metallic Materials: Used in specialized applications where resistance to chemicals or extreme temperatures is critical, such as in the pharmaceutical or food industries.
2. Pressure And Temperature Ratings
When choosing flanges, you need to look at their pressure and temperature ratings. These tell you how well they can handle operational situations without breaking. Factors to consider include:
Pressure Class: Indicates the maximum pressure that the flange can withstand at a given temperature range.
Temperature Range: Lists the highest and lowest temperatures that the flange can still be structurally sound.
By knowing these values, you can be sure that the chosen Hastelloy C276 Flanges can work safely within the environment’s pressure and temperature limits.
3. Corrosion Resistance
In many industrial settings, corrosion is a big problem, especially where chemicals, salt water, or high humidity are present. Choosing flanges with adequate corrosion resistance properties minimizes the risk of degradation and extends the lifespan of the piping system. Factors influencing corrosion resistance include:
Environmental Exposure: Assessing the presence of corrosive elements such as acids, alkalis, salts, and humidity.
Coatings And Surface Treatments: Applying protective coatings or treatments like galvanization, epoxy coatings, or polymer linings to enhance resistance against corrosion.
4. Environmental Conditions
The specific environmental conditions where the flanges will be installed play a crucial role in selection. Factors to consider include:
Outdoor Vs. Indoor Installation: Outdoor flanges may require additional protection against weather elements and UV exposure.
Exposure To Chemicals: Flanges in chemical processing plants must withstand exposure to corrosive chemicals and high temperatures.
Hygienic Requirements: Flanges used in food processing or pharmaceutical industries must meet sanitary standards to prevent contamination.
5. Size And Dimensional Considerations
Flanges are available in various sizes and dimensions to accommodate different pipe sizes and configurations. Ensuring compatibility between the flange dimensions and the piping system is essential for proper installation and functionality.
6. Installation And Maintenance Requirements
Flanges work best and last the longest when they are installed correctly and are maintained on a frequent basis. Considerations include:
Bolt Tightening: Following recommended torque values to achieve proper sealing and prevent leaks.
Inspection And Testing: Conduct periodic inspections and pressure testing to identify potential issues and ensure compliance with safety standards.
Replacement And Upgrades: Upgrading flanges as needed to adapt to changes in operating conditions or to comply with updated industry standards.
Conclusion
Selecting the right Inconel 600 Flanges for different environments involves a careful assessment of material properties, pressure and temperature ratings, corrosion resistance, and environmental factors. Industrial facilities can make their piping systems work better, last longer, and be safer by knowing these important factors and following best practices for installation and maintenance. It is important to buy high-quality flanges that are right for the job in order to keep downtime to a minimum, lower upkeep costs, and make sure that equipment works reliably in a variety of industrial settings.